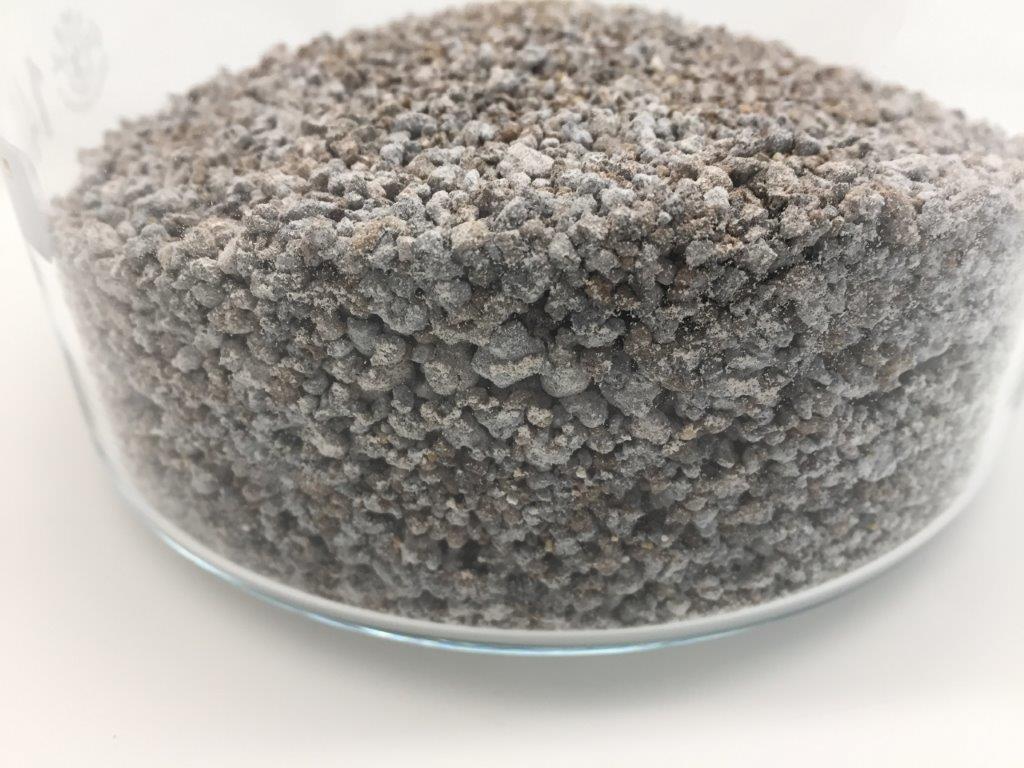
Unique selling points
- Output with high plant availability that can be sold as a fertiliser raw material
- Small-scale process that can be integrated onsite on WWTP
Description of the technology
The Pyrophos® process jointly developed by FHNW, CTU AG, AVA Altenrhein, FiBL and Landor is a multi-stage thermochemical process for sewage sludge via fluidized bed pyrolysis with subsequent post-combustion (Schaub et al. 2019). It is usually applied at wastewater treatment plants with a capacity of 100 000 population equivalents and greater. This corresponds to a loading rate of 1 t dry matter/h and higher.
Depending on the output requirements and availability, drained or dried sewage sludge, animal meal, animal meal ash or other phosphorus containing waste with low heavy metal pollution can be used as raw materials. The phosphorus containing raw materials are mixed with a potassium salt as an additive to improve the plant availability of the phosphates and fed into the reactor (Fig. 1). In the process, the heavy metals, which are volatile under reducing conditions, are partially expelled via the gas phase and retained in the exhaust gas cleaning system. At the same time, the thermal process converts the poorly soluble phosphates in the raw materials into potassium phosphates with a high solubility of over 80% in neutral ammonium citrate (NAC). Phosphoric acid can be used to stabilise the quality of the output. A post-combustion process produces ash containing potassium and phosphate, which can be processed into a multi-nutrient fertiliser.
Similar processes for phosphorus recovery are the ASH-DEC and the Euphore process. Thermal treatment of sewage sludge and other phosphorus containing organic wastes generate heat and typically reduce the carbon content to less than 1% thus eliminating most organic pollutants. Heavy metals are partially eliminated by evaporation either in elemental form (reducing conditions for mercury) or as metal chlorides (therefore, the addition of a chloride donor is needed). By adding alkaline metals, the phosphate form can be modified and solubility and thus plant availability be improved.
Flow scheme of the technology
Fig. 1 Flow scheme of the thermal treatment technology applied in the NextGen project
Pictures
Synergetic effects and motivation for the implementation of the technology
- Removal of contaminants due to the thermal treatment with chloride addition
- Recycling of phosphorus
- Disposal and P recovery also decentralized and possible for smaller amounts of sewage sludge
- Profitability strongly dependent on energy usage options at the location
- Potential for cost reduction by using the heat recovery and exhaust air purification of an existing incineration plant
Technology requirements and operating conditions
The Pyrophos process requires a high content in total solids of at least 75%. The temperature for the thermal treatment ranges between 700 °C and 1000 °C. Depending on the compositions of the sewage sludge, a maximum total phosphorus (P) content of 60 g/(kg TS) can be achieved. Potassium is added with a ratio between 2 and 4 kg K per kg P.
Parameter |
Units |
Min |
Max |
Reference |
Total phosphorus |
g/(kg TS) |
- |
60 |
NextGen D1.5 (in prep.) |
Total solids |
% |
75 |
- |
NextGen D1.5 (in prep.) |
Temperature |
°C |
700 |
1000 |
NextGen D1.5 (in prep.) |
Potassium addition |
kg K/ (kg P) |
2 |
4 |
NextGen D1.5 (in prep.) |
Key performance indicators
Besides the P-recovery rate and the P and K contents of the PK-fertiliser, also the solubility in neutral ammonium citrate (NAC) is shown as a key performance indicator. This solubility with the abbreviation PNAC is an indication for agronomic effectiveness of the fertiliser in terms of phosphorus and a requirement of the European fertiliser products regulation.
Parameter |
Units |
Min |
Max |
Reference |
P-recovery rate of soluble phosphates (influent WWTP) |
% |
90 |
100 |
NextGen D1.5 (in prep.) |
PNAC of ash from sewage sludge |
% |
>80 |
NextGen D1.5 (in prep.) |
|
P2O5 content of PK-fertiliser |
% |
15 |
20 |
NextGen D1.5 (in prep.) |
K2O content of PK-fertiliser |
% |
12 |
16 |
Calculated with P2O5/K2O = 1.25-1.3 |
Links to related topics and similar reference projects
Thermal treatment |
Reference |
For PK-fertiliser production |
Case Study applying the technology
Publications
- Kleyböcker, A., Kenyeres, I., Poor-Pocsi, E., Nättorp, A., Loreggian, L., Schaub, M., Egli, C., Grozavescu, M., Murariu, M., Radu, B., Scheer, P., Lindeboom, R., Giurgiu, R., Suters, R., Heinze, J., Soares, A., Vale, P., Kim, J., Lanham, A., Hofman, J., D1.5 (2022) New approaches and best practices for closing materials cycle in the water sector, 2022
- Schaub, M., Stemann, J., Witgens, T., Verfahren zur Behandlung eines phosphorhaltigen Materials, 2019