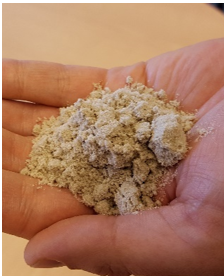
Unique selling points
- High phosphorus removal and recovery rates related to the influent to the recovery unit of up to 95%
- Struvite is a high quality product which can be used in agriculture as slow release fertilizer
- Reduced struvite scaling in pipes and pumps
- Significant reduction of the phosphorus return load
Description of the technology
In the wastewater sector struvite is usually used as a name for magnesium ammonium phosphate (MgNH4PO4*6H2O), even though it is the name of a mineral family. Struvite is a slow release fertilizer (Kratz et al. 2019) and all three nutrients are plant available as from mineral fertilizers (Watson et al. 2019).
Phosphorus removal and recovery via struvite precipitation is applied at wastewater treatment plants, usually after a pre-treatment such as anaerobic digestion or even a combination of anaerobic digestion with an additional hydrolysis such as a thermal pressure hydrolysis or a thermal alkaline hydrolysis in order to increase the dissolved phosphate concentration.
To enable struvite precipitation, a pH of 7.5 and higher is required. Hence, as a first step towards a higher pH, the CO2 is stripped via air injection. In a second step, caustics are added such as NaOH, if the CO2 stripping has not reached the required pH value. To induce struvite precipitation, together with a certain ammonium concentration, a magnesium source is usually added such as MgCl2, MgO or Mg(OH)2. Magnesium forms together with phosphate and ammonium struvite. This takes place in a reaction tank, the so called struvite reactor, which is typically a continuously stirred tank reactor. Crystal growth is promoted by mixing, sufficient retention time and recirculation of formed crystals. As a last step, the struvite in form of larger crystals is separated in a settling tank. Usually, the struvite is dewatered, dried and processed, before it can be applied as a slow-release fertilizer.
Variants of the process: sludge - liquor
If the CO2 stripping and struvite precipitation take place in the sludge, the separation of the struvite crystals is less efficient and the crystals are usually inhomogeneous due to organic and/or inorganic impurities. However, the controlled struvite precipitation can be a useful measure to prevent pumps or pipes in the sludge line from scaling or even clogging (Desmidt et al. 2015).
If the CO2 stripping and struvite precipitation take place in the liquor (e.g. after dewatering), the subsequent separation of the struvite is very efficient. However, the higher phosphate concentrations are, the lower the dewatering efficiency of the upstream dewatering unit is (Kuhn et al. 2013). Thus, the dewatering step might require more energy and sometimes even additives such as polymers in order to reach the required liquor quality. In the liquor, the crystals grow usually homogeneous. In NextGen the focus is on struvite production in the liquor, hence, the following sections will focus on this technological solution only.
Flow scheme of the technology
The flow scheme shows an example for struvite production in the liquor. After CO2 stripping, the struvite crystals precipitate in the struvite reactor as already described. Macro crystals settle down ready to leave the struvite reactor and micro crystals (struvite nuclei) are distributed in the liquor and enter the settling reactor. There, they can further grow and settle down. However, if they are still too small for settling, they are transported back to the struvite reactor. The hydrocyclone separates the small crystals from the liquor. They serve as struvite nuclei and lead to an improved crystal growth within the struvite reactor. The system of the reactors is very flexible, shown by the dotted lines that indicate an alternative way of operation.
Pictures
Synergetic effects and motivation for the implementation of the technology
- Reduction of the phosphate return load of a WWTP
The WWTP profits from the reduced phosphate return load. Thus, a part of iron or aluminium salts often used for a conventional chemical removal might be saved due to the lower return load.
- Prevention of clogging events in pipes
Depending on the chemical composition of the wastewater and the pH conditions, struvite can precipitate in undesired parts in the wastewater treatment plant e.g. in pipes leading to scaling and clogging. Due to a controlled removal of the phosphate from the liquor, those processes will be diminished or even avoided in the subsequent plant parts.
Technology requirements and operating conditions
In order to reach high struvite yields, the dissolved phosphate concentration in relation to the total phosphorus content should be as high as possible in the reactor influent. At least the concentration should be at 50 mg PO4-P/L, while the total suspended solids (TSS) and total solids (TS) should be below 600 mg/L and 2%, respectively. Furthermore, ammonium and magnesium need to be present. Therefore, a molar ratio of Mg:N:P between 1:2:1 and 1:12:1 should be maintained in the reactor.
Parameter |
Units |
Min |
Max |
Reference |
PO4-P |
mg/L |
50 |
- |
|
TSS |
mg/L |
- |
600 |
NextGen D1.5 (in prep.), Ohl 2020 |
TS |
% |
- |
2 |
NextGen D1.5 (in prep.), NuReSys 2020 |
pH |
- |
7.5 |
9 |
NextGen D1.5 (in prep.), Cornel and Schaum (2009), Shaddel et al. (2019) |
Mg:N:P molar ratio |
- |
1:2:1 |
1:12:1 |
Key performance indicators
Besides the P-recovery rates, also the solubility of struvite in neutral ammonium citrate (NAC) is shown as a key performance indicator. This solubility PNAC gives a hint to the plant availability and agronomic effectiveness of the fertilizer.
Parameter |
Units |
Min |
Max |
Reference |
P-recovery rate |
% |
90 |
95 |
NextGen D1.5 (in prep.) |
P-recovery rate |
% |
10 |
20 |
NextGen D1.5 (in prep.) |
PNAC |
% |
69 |
96 |
Links to related topics and similar reference projects
Phosphorus recovery processes |
Reference |
Struvite production |
|
Hydroxyapatite production |
Case Study applying the technology
Publications
- Cornel, P., Schaum, C., Phosphorus recovery from wastewater: needs, techniques and costs, 2009
- Desmidt, E., Ghyselbrecht, K., Zhang, Y., Pinoy, van der Bruggen, B., Verstraete, W., Rabaey, K., Meesschaert, B., Global phosphorus scarcity and full-scale P-recovery techniques, 2015
- Kleyböcker, A., Kenyeres, I., Poor-Pocsi, E., Nättorp, A., Loreggian, L., Schaub, M., Egli, C., Grozavescu, M., Murariu, M., Radu, B., Scheer, P., Lindeboom, R., Giurgiu, R., Suters, R., Heinze, J., Soares, A., Vale, P., Kim, J., Lanham, A., Hofman, J., D1.5 (2022) New approaches and best practices for closing materials cycle in the water sector, 2022
- Kratz, S., Vogel, C., Adam, C., Agronomic performance of P recycling fertilizers and methods to predict it: a review, 2019
- Kuhn, E., Rensch, D., Haueter, R., Kopp, J., Stand der Technik für die (mechanische) Entwässerung von Klärschlamm, Ermittlung und Beschreibung, 2013
- NuReSys, Reference projects, 2020
- Ohl, S., Klärwert, 2020
- Shaddel, S., Ucar, S., Andreassen, J., Østerhus, S., Engineering of struvite crystals by regulating supersaturation – Correlation with phosphorus recovery, crystal morphology and process efficiency, 2019
- Watson, C., Clemens, J., Wichern, F., Plant availability of magnesium and phosphorus from struvite with concurrent nitrification inhibitor application, 2019